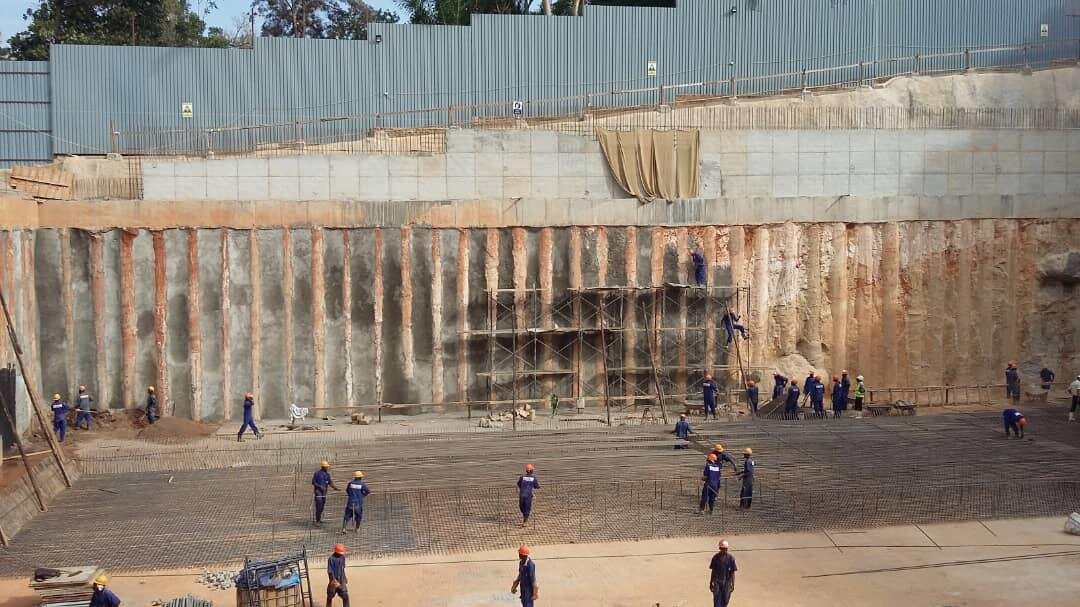
PPDA Building: Contiguous Pile Wall, December 2018
Scope of Services:
Installation of 800mm and 1100mm rotary piles to form a contiguous pile wall around a 3 storey basement, approximately 50mx50m
Location: Nakasero Rd, Nakasero Kampala
Completion Date: December 2018
Main contractor: Seyani Brothers
Client: Government of Uganda
Project Description:
EAP mobilised a Soilmec R620 rotary piling rig to install the piles at the site in central Kampala. The main contractor had excavated the inclined plot down to a formation level at the road Level but needed to excavate a further 10m to achieve the basement design.
The design work was complicated by the existence of an eight storey building on the adjacent plot with its wall very close to the proposed excavation. During tender stage some investigation had been completed to demonstrate the extent and competence of the foundation for this building but being not without some anomalies the pile wall was designed to take considerable load from the building.
Initial designs featured soil nails and ground anchors to support the vertical piles on other sides of the plot but these were disallowed by the neighbours to the front and rear. A full cantilevered approach was thus adopted for all four sides.
As soon as work got underway the challenges mounted. Ground investigations had indicated that no rock was to be found at the pile depth but rock was found on the first day of drilling not only with the design depth of the piles but within the design depth of the basement. More extensive investigation revealed a sloping bedrock that varied considerably in depth across the plot. New design critera were sought and tools to drill through the rock were mobilised.
Even then, some rock encountered was more than double the strength reported by the ground investigation. EAP mobilised a small down the hole hammer in order to penetrate a very strong isolated boulder located just a few metres under the formation level that had not been picked up by the ground investigation.
Steel cages were fabricated on the site by the main contractor were loaded into the open bore by EAP using an all-terrain crane. Concrete was batched at the main contractor’s off-site batching plant. EAP used an 8inch tremie pipe system to install the concrete. The concrete was filled from concrete mixer trucks directly into the tremie hopper.
The pipes were lifted into position using the all-terrain crane.